A quick guide to help contractors on the job.
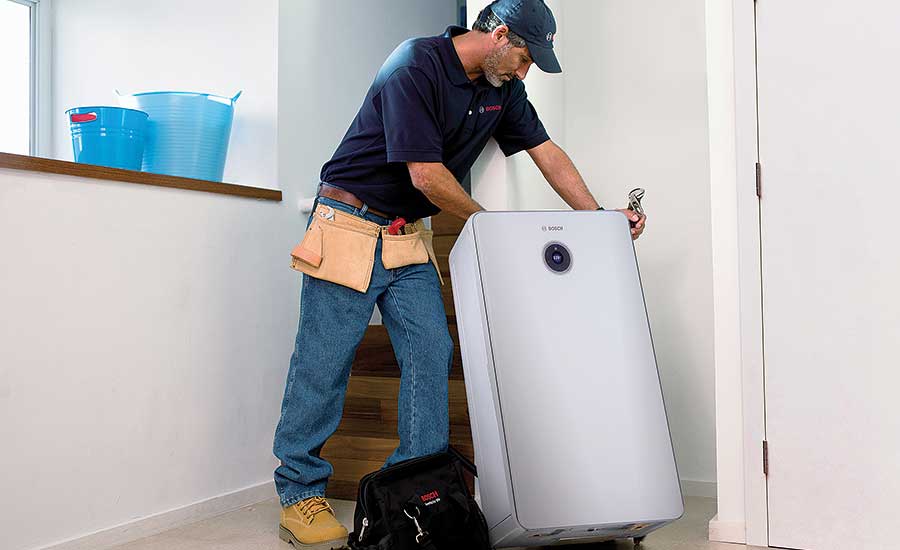
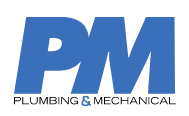
Unlike their traditional storage tank-based counterparts, tankless water heaters are capable of providing a constant flow of hot water on-demand. The concept is relatively simple: The heaters function by coupling a modulating burner with a high-efficiency heat exchanger.
Given their higher efficiency, these heaters are an effective way to save on energy consumption: End users can typically conserve up to 40% in annual energy costs versus tank-type water heaters; making them attractive to both eco-minded and budget-conscious customers.
These two factors make tankless water heaters popular with consumers, and with the right strategy, contractors can help their customers reap the benefits, whether with new construction or a retrofit upgrade.
Be comfortable with the product
Here are four tips that will help contractors when installing and servicing tankless water heaters:
1. Review the manual prior to installation. This is 101-level advice, but it is painful to hear about mistakes that should have been avoided, so it bears repeating: The most important thing a contractor can do for himself or herself (and the customer) is to get comfortable with the product he or she will be installing. The best way to do this is through the manufacturer’s installation manual/brochure; no one knows the product better than the manufacturer, so don’t take this resource for granted.
If the product is new to you and you have never installed one, don’t read the manual the morning of installation. An ideal scenario is having the appliance delivered in advance and reviewing both the product and the manual ahead of time to get the lay of the land. An even better way to become familiar with a product is attending a manufacturer’s training class, where you can see the product before delivering it to your customer.
2. Use troubleshooting best practices. Familiarity with the installation manual comes in handy when troubleshooting and servicing. Without a base knowledge of the manual and the ability to follow manufacturer-recommended servicing flow charts, a contractor might replace a part without knowing that particular part was the culprit — and that can lead to a frustrated homeowner who needs to call for service yet again.
Additionally, the new high-efficiency products on the market don’t necessarily have the same indicators older products have; they instead show an error code, just like a car with a “check engine” light on will when plugged into a diagnostic system.
Of course, learning the error code does not always close the loop on a diagnosis; often, issues that show up in the function of the unit are a result of problems elsewhere in the unit’s gas, venting or plumbing. When that happens, don’t be afraid to call the manufacturer directly. Every manufacturer has a call center with people who can help guide a contractor over the phone.
Be sure to have the troubleshooting guide nearby, as one of the first questions support personnel will ask is what manufacturer-recommended steps you have already taken to prove something has failed. Additionally, when you call for help, the first thing the technician on the phone will ask is the unit’s model and serial number.
While the call might seem excessive or time-consuming, think of it this way: If you misdiagnose a problem on an appliance that continues to fail, your reputation with the homeowner will suffer, and review sites like Angie’s List, combined with good old-fashioned word-of-mouth, may impact your reputation beyond that single customer. It’s better to get the help you need to get it fixed the first time, rather than risk your professional reputation.
3. Perform regular maintenance service checks. Performing routine maintenance is a key component for high performance and a long service life. While a conventional water heater typically requires replacement every seven to 10 years, a tankless model could last up to 20 years with recommended annual maintenance.
Annual maintenance includes inspecting the venting system, combustion chamber, burner, pressure relief, water filter and condensate trap. Many manufacturers’ maintenance requirements include descaling the heat exchanger yearly and cleaning the fin coils of the heat exchanger every two years. Examine the water heater and its components for wear or fatigue, and immediately repair all faults to avoid damage to the system.
Remind your customers that just like checkups at the doctor and car inspections at the auto shop, routine maintenance on tankless water heaters helps address any repair issues early and ultimately extends the life of their unit.
When troubleshooting and performing maintenance, develop a routine. The more you perform that routine, the fewer times you will forget to check and double-check something. If you can trace every possible service situation you perform in a direct line from step A to B to C to D, and so on, you’ll never miss a step.
Some tankless-specific maintenance tips include:
- Water quality can have an impact on appliance longevity, and poor quality may void the manufacturer’s warranty. Before installing a unit, call the local water department for water analysis data, or, have the homeowner analyze their well water if on a well.
- If the tankless water heater is operating in applications where the outlet temperature exceeds 140° F, a water softening system is strongly recommended. The higher the set temperature is on the appliance, the greater the risk for scale/mineral deposits.
- In areas where the water supply has a high mineral content, the heat exchanger should be flushed with a descaling solution. Scale buildup will shorten the life of the water heater, and damage resulting from scale may not be covered under the manufacturer’s warranty. A water softener is required if the water hardness exceeds 6 grains/gal (180 mg/l) calcium carbonate.
In addition to routine maintenance, contractors should encourage their customers to winterize their tankless water heaters for seasonal use. If the unit must be installed in a location where it may be exposed to freezing temperatures, all the water needs to be drained from the heater. For full details on maintenance and winterizing tankless water heaters, always consult the manufacturer’s installation and maintenance instructions.
4. Never stop learning. Don’t be afraid to learn about new appliances. Contractors who have been in the business for decades might have no desire to learn how to install and repair the newer high-efficiency equipment, but it’s what most homeowners want these days, and contractors looking to maintain or grow their business will need to roll with the punches and get familiar with the new appliances. Technology is changing at an amazing rate; think about the type of products being installed just 20 years ago compared with the products we see in supply houses today.
When it comes to learning to install and repair new appliances, contractors have resources. Manufacturers offer training sessions to get technicians familiar with their specific products, and it’s a good way to learn about the equipment through firsthand experience. Some manufacturers will travel to you, while others might prefer to work in their own labs. Either way, there are plenty of options for contractors who want to gain more experience with a particular manufacturer’s appliances.
Remember, there is no such thing as a stupid question. Manufacturers are motivated to ensure that the contractors installing and servicing their equipment are doing so correctly, and their support staff will be more than willing to help with any question or issue you encounter – after all, their reputation is on the line, too.